membrane Filter Press
Filter press is a very strong and functional filter that is used to purify residues, sludge and other liquids requiring purification. In order to use this type of filter, recognizing the type of sludge and sensitivity of the type of purification or dewatering type is very important and should be chosen in proportion to the type of sludge of these filters. The main advantage of membranes filter press can be much better dewatering and production of dried sludge cake with high concentration.
The structure of filter presses is that apart from fixed plates that have high strength, other flexible filter plates are used that have the ability to withstand a lot of pressure, which is called flexible filters.
In this type of filters, in the first step, the sludge loading is done by the filter press, and then with the pressure of the residual liquid air, the residual liquid is pushed into the membrane part of the membrane, the sludge is treated to much more pressure and the water is dewatered and dewatered, and the water is treated with better quality and higher efficiency.
The important thing is that the design and manufacture of membranes filter press in industries is very different and is actually the type of project that determines the structure of these filters. This has caused most of the filter presses for industries to be customized because first, a detailed expert of the type of industry has been done and the best type of filter press according to the type of industry is considered and produced for the manufacturing workshop.
In this article, we are going to familiarize you with all aspects of filter press. The full study of this section takes approximately 30 minutes. If you wish, instead of reading this article, please contact our experts right now to answer all your questions for free.
In this article, we are going to familiarize you with all aspects of filter press. The full study of this section takes approximately 30 minutes. If you wish, instead of reading this article, please contact our experts right now to answer all your questions for free.
Contents
Advantages of Membranes Filter Press
Excellent results that the purification process with membranes filter press has brought with its membrane filters and the possibility of localization of this type of filter for different industries has caused many production programs to tend toward the use of these filters. Today, a large number of industries have considered the use of filter press membranes due to higher productivity of their work processes and seeking to reduce their side costs, including mining, chemical or pharmaceutical industries.
Even in order to meet the various needs of the industry and activities related to the municipality, the membranes filter press have used MSE membranes in their modular design in the press chamber. The frame of these presses is considered to be hard and heavy and consists of components such as: the power supply of the stands with the filter output (head of the machine), hydraulic bases with cylindrical lock (pressure piece), columns or cross beams and side rails placed on them.
Membrane filter plates are individually designed and adjusted. The plate press fabrication is composed of uniform membrane plates (it is also possible to use a combination of membrane filters in the chamber) and uses a 50-15mm cutter to make the sludge cake.
The membrane materials used in the production of these filters are standard polypropylene (PP) materials, synthetic rubber e.g. NBR, EPDM or TPE elastomer. Special materials such as PVDF are used in the structure of these filters. Membrane press filters using membrane technology in their filter plates will have a great impact on the remaining solid dryness. Compared to conventional filtration processes, these filters leave the lowest moisture content and leave a drier cake. This has turned membrane membrane membrane filter or membrane filter membrane membrane membrane filter into a very powerful and widely used system in various industries.
Membrane technology as a great solution if the time and degree of water treatment is of great importance
Depending on the amount of water pollution and the amount of dehydration required, the residual dry matter content (both the dryness of the remaining cake and the weight percentage of the dry matter in the filter cake) can be achieved by compressing the membrane plates in the filter cake. The range of dry content available in this type of filtration can be extended between 30 and 80 percent. In the standard version the pressure is applied from both sides. Sludge or liquid clamps that need to be refined can also be used for each problem in the second filtration process.
The combination of membrane filters and enclosure plate filters can reduce your costs and easily even guarantee excellent filtration in your work process.
In this type of filter, the process of releasing the cake produced by a toggle is easily done. In addition, to prevent contamination, dripping is prevented by using a special tray and parts such as backup platform, backup structure, manual ladder and automatic gasket are also used in the structure of the filter press machine.
Components of membranes filter press
In general, the filter press machine includes the following main components:
- A metal plate or mold that will usually be simple iron or custom alloy. This mold or home plate is the same as the main body or trunk of the material charger.
- The main hydraulic platform that works by opening and closing plates using cylinders as well as increasing pressure on the membrane plates of filter presses
- The rail part of the device that holds robotic rails and suction. This part of the rail is used to move the membranes and after draining the cake water, the membranes are opened and separated using the same rail so that the resulting cake can be drained.
The main advantages of using membranes filter press in various industries
Perhaps we can dare say that themembranes filter press show us their true meaning at the time of rinse and to adjust the degree and time of rinsing. However, the main advantages of compressed membrane filter can be defined as:
- Depending on the desired degree of rinsing of the processed cake, the desired result can be achieved by compressing the membrane plates. The rinse interval or dryness of the cake can be between 30 and 80 percent. In standard mode, the amount of rinse can be obtained bilaterally by compressing the press plates.
- One of the main advantages of filter presses is that it does not only show the quality of its work in compression, but also can be seen in reducing the compression time. In general, the membrane filter performs filtration work for up to half the time and increases the production efficiency by 50%.
- In standard mode, expansion pressure can be increased up to 15 open pressures, and even under certain conditions, the pressure can be adjusted much higher on numbers.
Steps of membranes filter press
The combined and operational cycle of membranes filter press can be described as summarized as follows:
- Closing Filter Press
- Loading or feeding Kuwaitis
- Cake Formation
- Compressing and optimizing the quality of cakes to a defined degree
- Filter Opening
- Drain cake
Ability to compress themes in membranes filter press membanes
In order to achieve better and better quality, the add-on compression method can be used in membranes filter press . In fact, the better performance of membranes filter press depends on the compression method. The degree of this compression is a function of particulate matter in the slurry. In fact, proper rinsing during compression gives us more confidence for the function of membranes. In order to obtain higher quality during cake rinsing, compression operations should be performed to enhance the quality of the cake rinse. This operation includes the following steps:
- Shastashvi Members
- Using air pumping on filters
- Rinsing the core of the membrane filter and pumping compressed air on the core
Remember that at the time of filter washing, the piece must be pressed in advance to ensure the filter stability is performed and prevent cracks or gaps on the filters during elongation.
Structural Design Filter Press
- Pressure system for closing the cylinder type of heavy duty upper jack
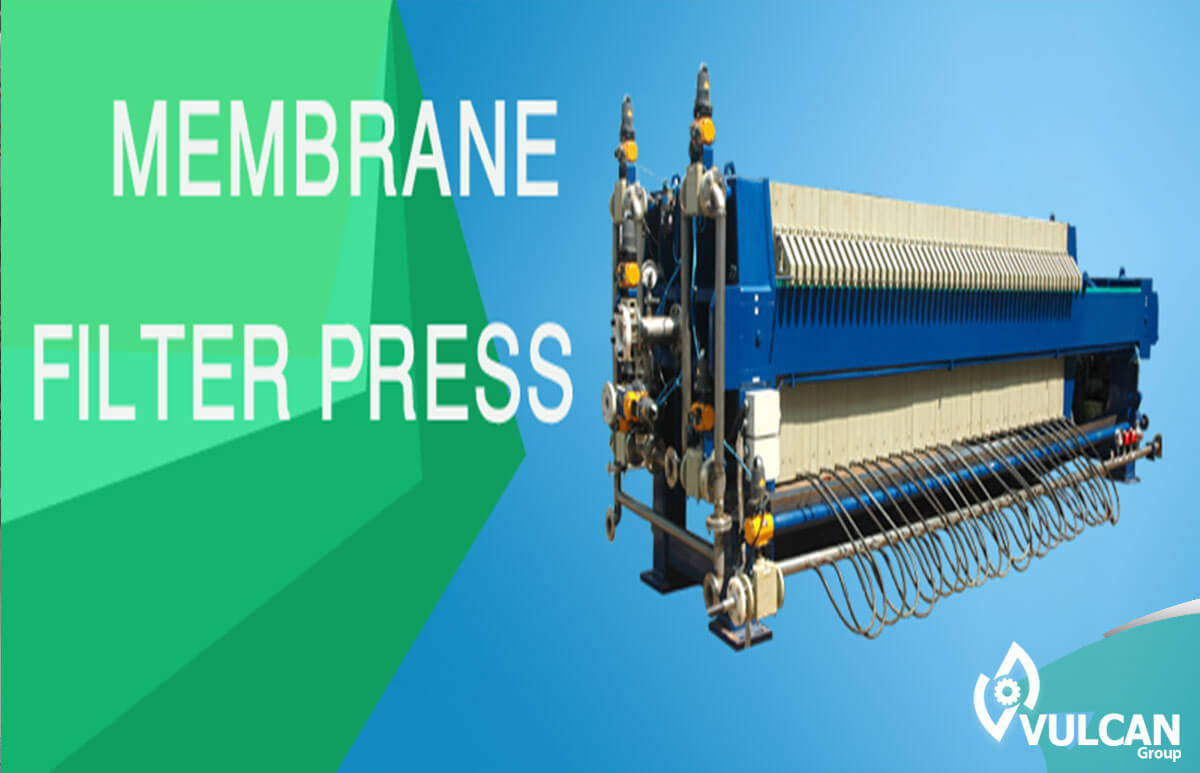
- Tensile system for closing the type of medium range upper jack cylinder
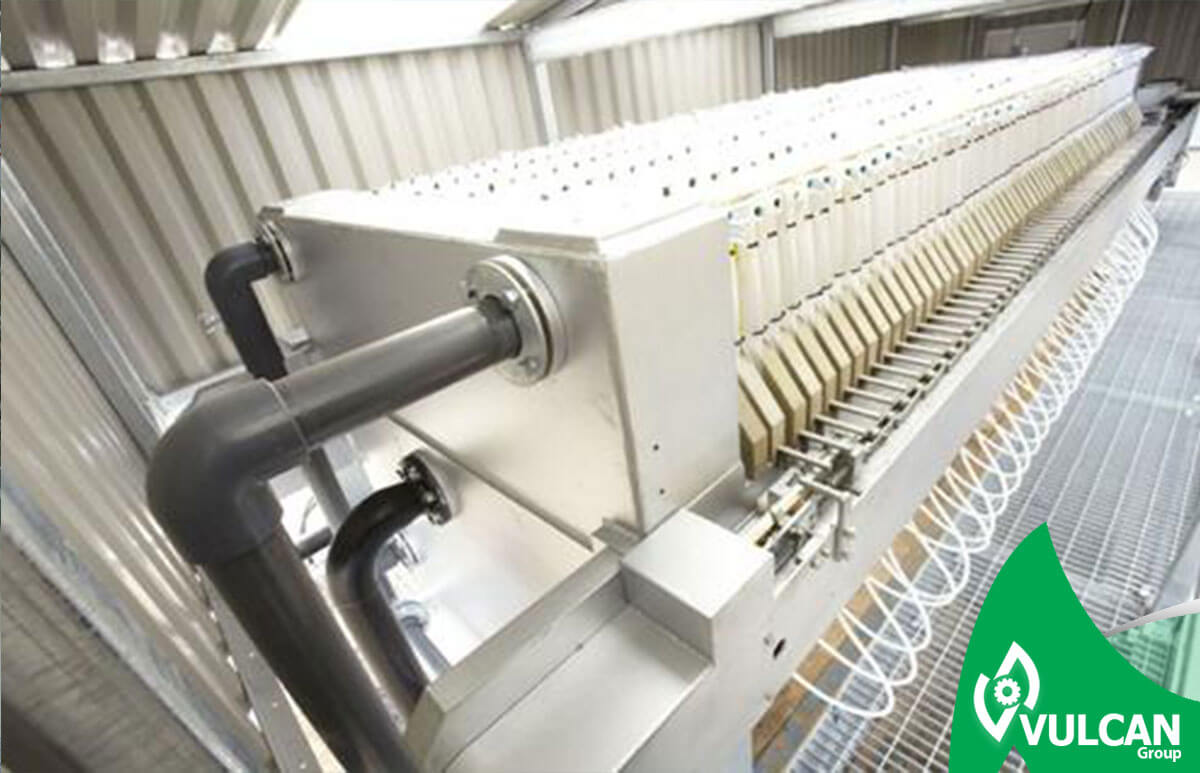
- Tensile system for closing the type of minimal side cylinder
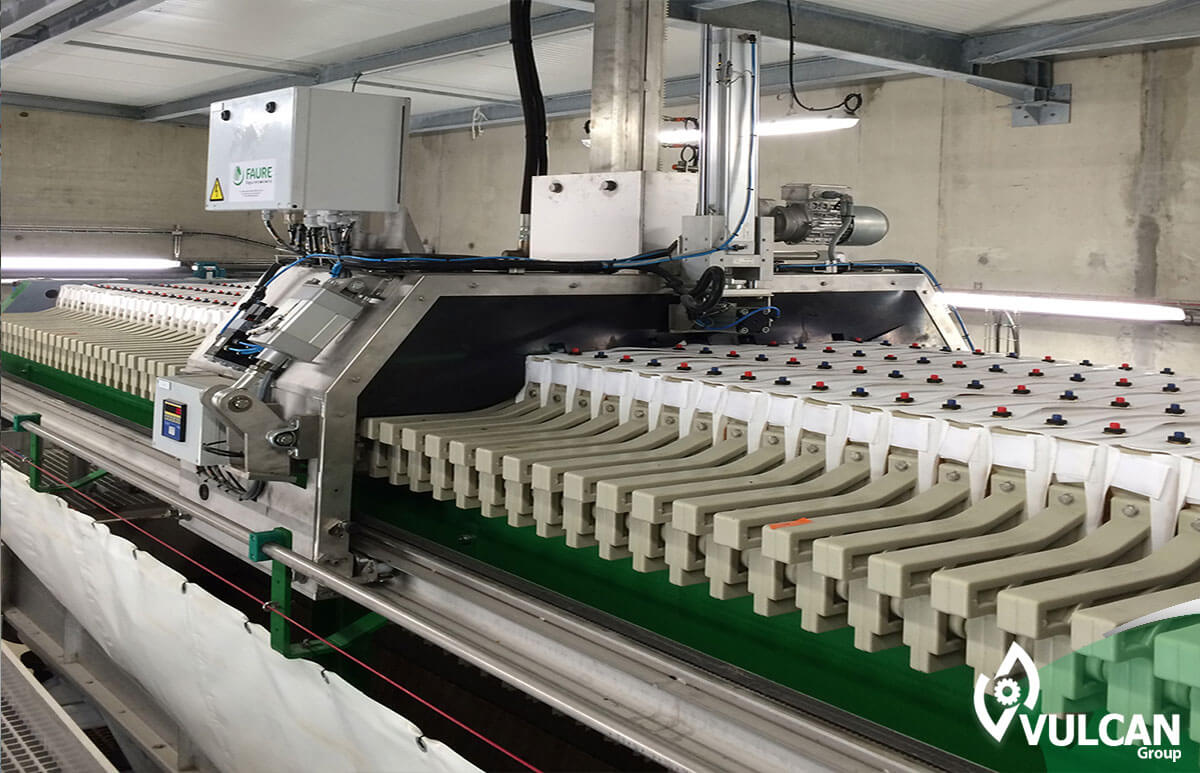
Wide range of filter presses
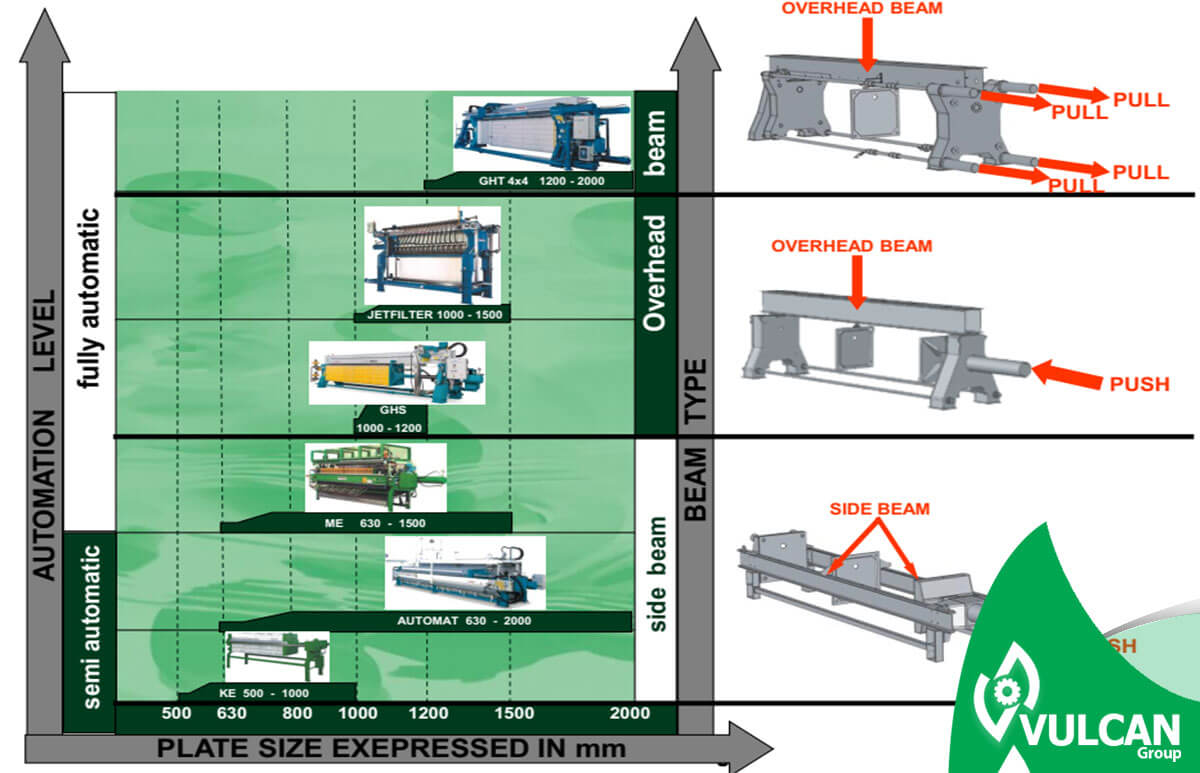
Portable filter presses
Advantages of removable filtration units:
- They were compact.
- Complete factory for all applications
- Easy access of personnel to the factory, both for operation and maintenance
- Has a wide range of applications using different sludge ventilation methods
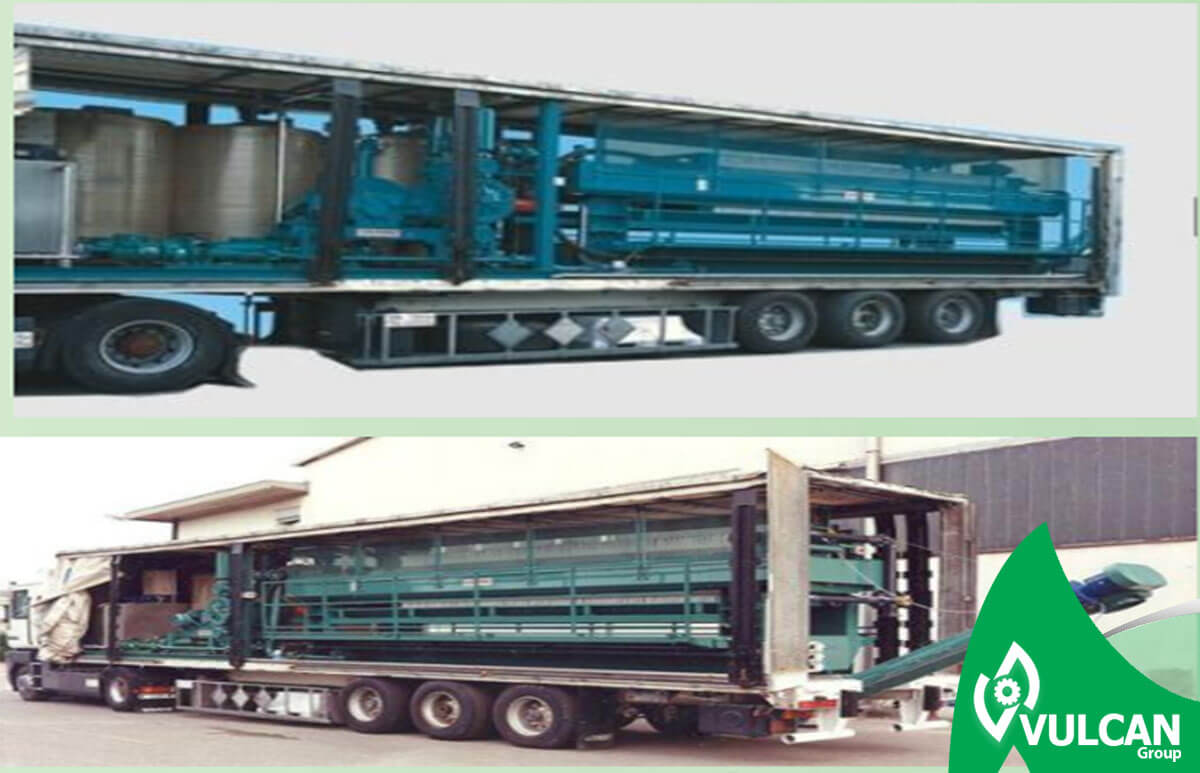
Membrane Filters
Each filter press model can be equipped with:
- Full rubber membrane plates
- Pages Chimber Perfect
- Synthesis Pages Members Elastici and Chimber
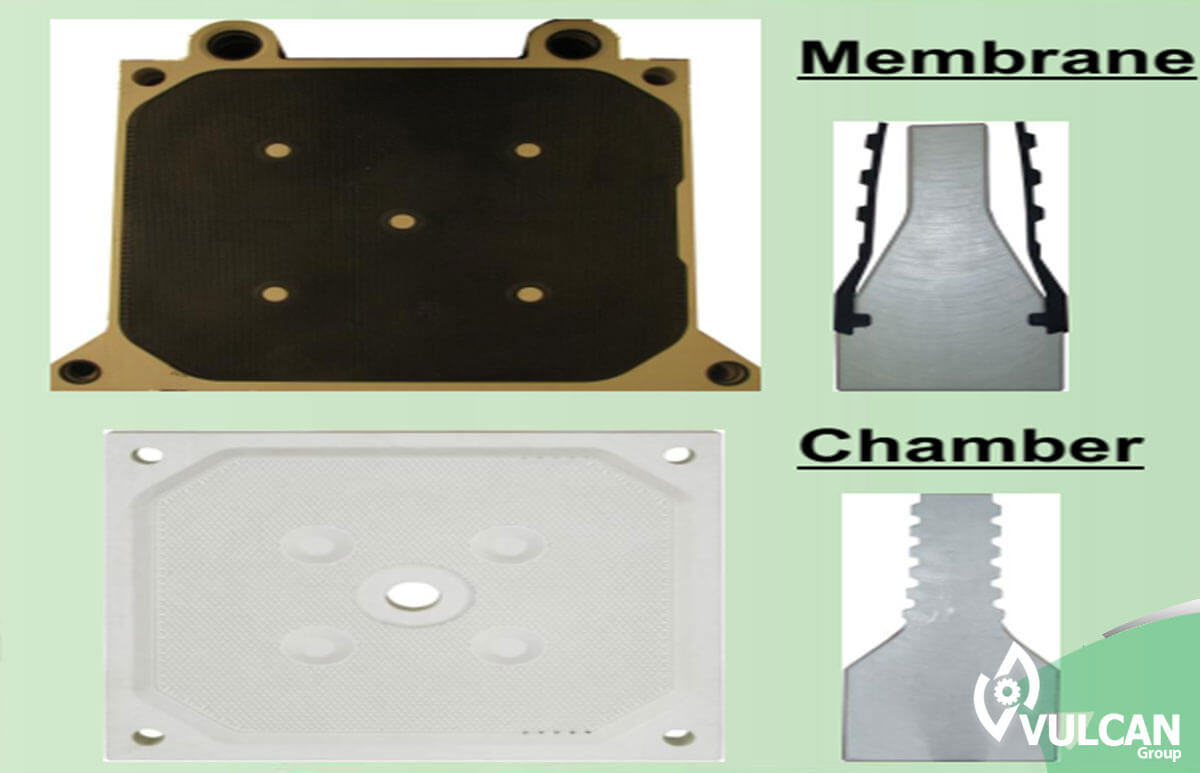
Autobiography and history of piece construction in Vulcan Group
THE TOP FILTER MANUFACTURERS WITH THE METHOD OF MSE AND JVK COMPANIES FROM GERMANY AND METSO MINERAL FROM THE SWEDISH CONSERM ARE. The remaining manufacturers are mainly manufacturers of chamber filter presses and belong to the People’s Republic of China.
The spark of production of the strategic piece of membrane filter press in Vulcan Group was created in January 1396. The obvious point of this plan is the employer’s own method based on R&D. In other words, it became operational with a view to the action of resistance economy and construction inside this project.
Due to the existence of appropriate infrastructure in the molding section of Vulcan Group and the use of modern mold making machines such as CNC in the open and more important expert human resources which is considered to be the most important spiritual capital of the organization, with a mere 500 hours of optimal working hours, the complex mold construction plan was possible.
Using powerful press compiling 1800-2000 tons with dimensions of 3.2*1*5 meters pilot design with a limited number of tried and error was successfully passed and the final piece was produced.
Design and fabrication of Teflon membrane membrane (Membrane Filter Plate)
Building an element from a component alone does not help localization. In practice, the rest of the parts will still be placed in the import bottleneck and the bottleneck of sanctions. Therefore, the Vulcan group, by identifying the strategic components of the filter press system, concluded that the construction of Tefloni Holder membrane is also of high importance and the demand for future production was always felt.
Considering the desirable infrastructures such as the mentioned at the beginning of the presentation, Vulcan Group, relying on expert workforce and up-to-date machinery in the shortest time, succeeded in feasibility studying the production and manufacture of the Tefloni holder sample of the membrane filter system.
Maximum power generation dimensions 2000(L)3000. (W) and test samples were successfully produced and emerged from the experiments.
In case of support of The National Copper Industries Company of Iran, such as past cooperation in the construction and localization of membranes filter press happened, Vulcan Industrial Group announces its full readiness to manufacture and produce Teflan plate filters.
Why is FilterPress strategic?
Filterpress system with membrane technology is one of the most up-to-date and technological methods in the world. All the most important companies in the world use this system in processing their available materials. In our country, Iran has a strong presence due to the multiplicity of large mines of this system.
The construction of this piece is limited to a few specific countries that do not exceed the number of fingers of one hand. For this reason, the bargaining power of the supplier is very high. In addition, due to sanctions and the need for mediation, the price of the piece for delivery in Iran is facing several times the price.
The high price of this piece is not due to the amount of consumables of this piece and in fact, the need for high technical knowledge for the production and molding of this very complex is the main reasons for this increase in price. In fact, the manufacturer of this piece has been selling technology rather than just a rubber piece.
Items and industries that use membranesfilter press
The importance of cake purification and production is seen in various industries. Nowadays, many industries, due to the high cost of filtration with old methods and lack of achieving their desired quality, see a lot of concerns in the quality and output of their work. Fortunately, the use of compressed filters or presses has covered a large volume of these concerns and by reducing the amount of failure and increasing the quality of work and reducing the time of cake production, it has yielded the best results for a variety of industries. Fortunately, with the localization of this type of filter in Iran and by Vulcan Industrial Group, access to these filters has been made possible inside Iran with indigenous knowledge and excellent after-sales service.
Membrane pages have special filtering elements with variable volumes. This has made it easy for all types of general and special applications to use filter presses.
The main industries that can and are suggested to use membranes filter press in their industry are the following:
- Mining & Ore Industries
- Metals (Iron, Nickel, Copper, Zinc)
- Non-metals
- Pure Metals (Gold, Silver, Platinum, Palladium)
- Coal Processing
- Calcium carbonate processing
- Minerals in general (silicate, clay, kaolin, etc.)
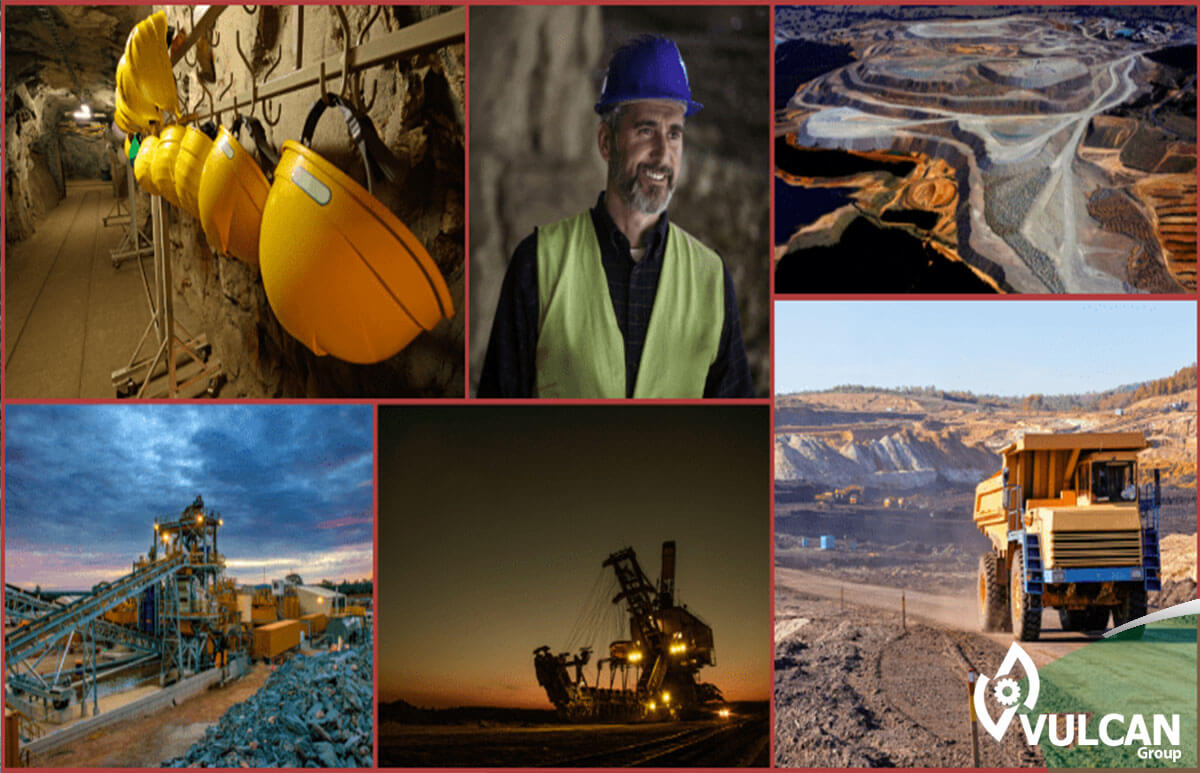
Mining Industry
Factory for filtering mineral concentrate (membrane filter press)
Dehydration of tailings of membranes or chambers or both
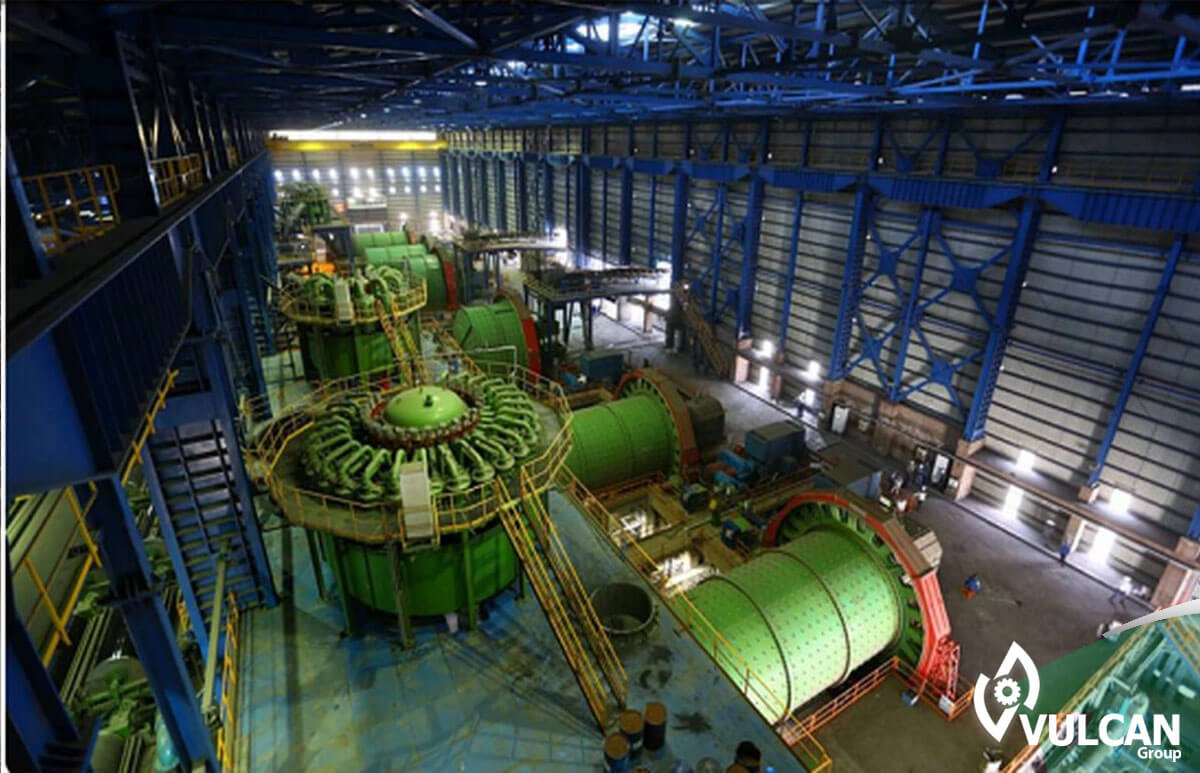
For mineral concentrate dehydration, filter presses are designed and produced, which are equipped with a combination of membrane and chamber plates.
Membrane plates have replaceable rubber membranes.
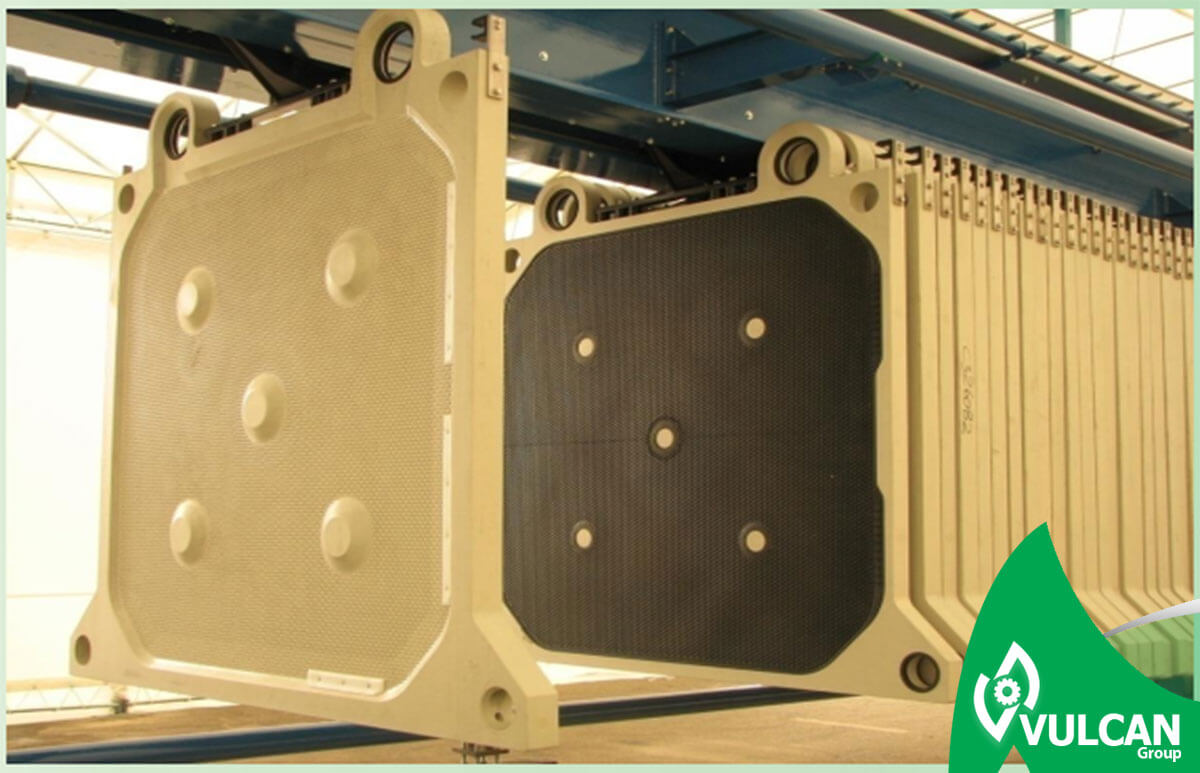
Filtration of ore concentrate
Due to the volume of concentrate produced, two different models of membranes filter press are designed:
- ME: Side cylinder model
- GHT 4*4: Upper cylinder model
Membran Filter Press
Using membranes filter press , high amounts of dry solids may be achieved: 91-95%
- The dehydratiation was resubmixed
Today, the management of waste and waste has become important in the mining industry for many reasons:
- Environmental Regulations
- Occupied space is tailings
- Water & Wastewater
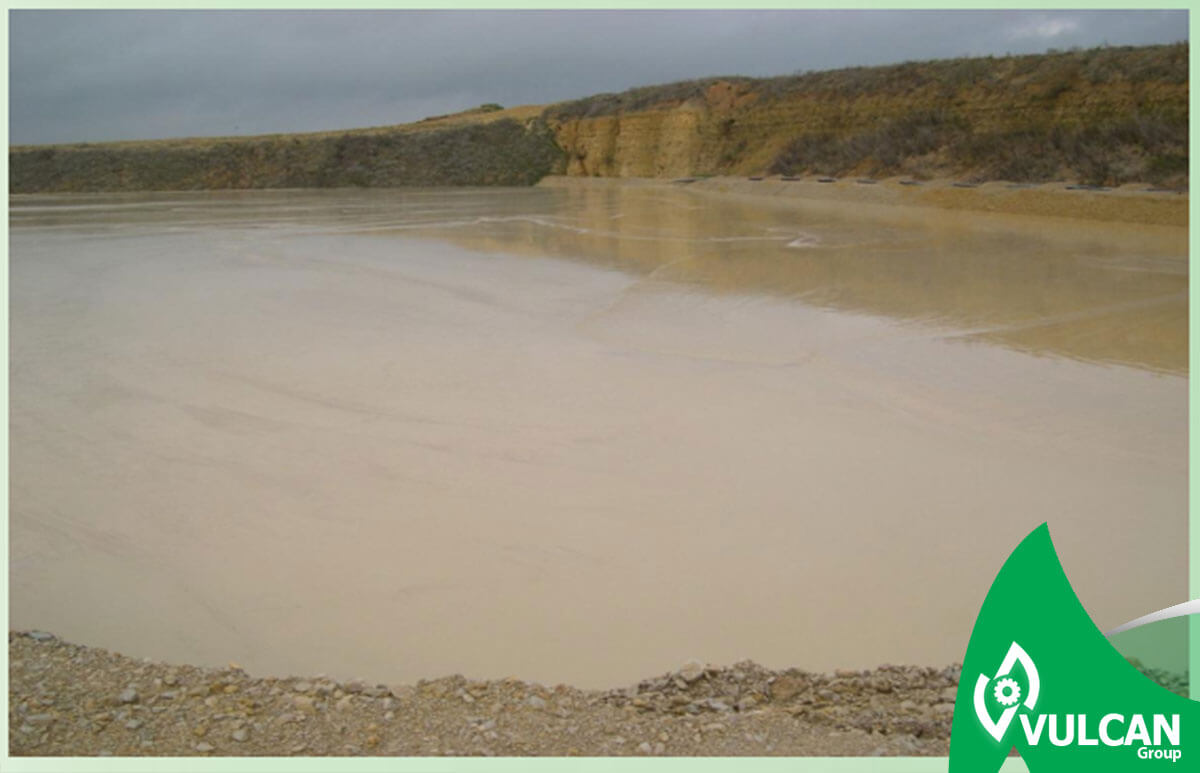
The dehydratiation was resubmixed
To meet these mining demands, create a press filter chamber with a long screen pack, which can be installed in a number of: 200 pages 2000 by 2000 mm
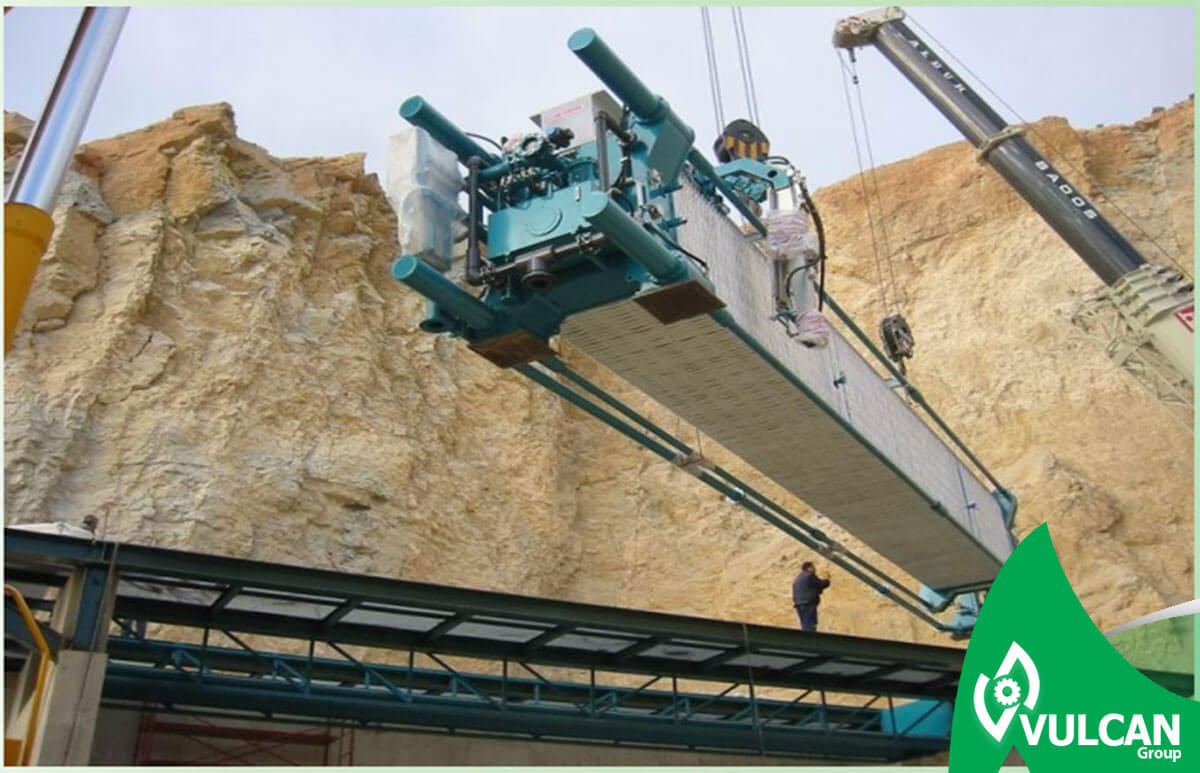
The main advantages of this method are:
Reduce the cost of investment
Water Recycling
Save Space
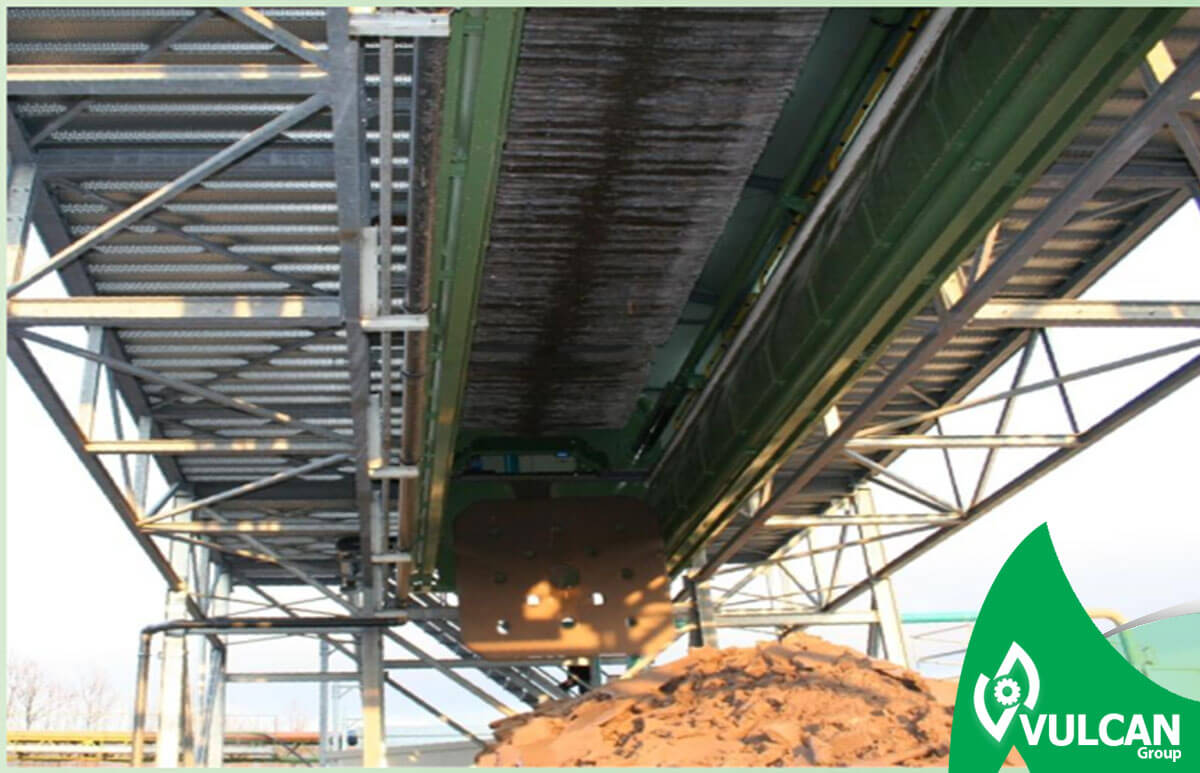
Metallurgical
- Hydrometallurgy
- Refining metals (zinc, copper, vanadium, chromium, manganese)
- Refinement of pure and rare metals (gold, silver, palladium, platinum)
- Steel factory and foundry (smoke purification)
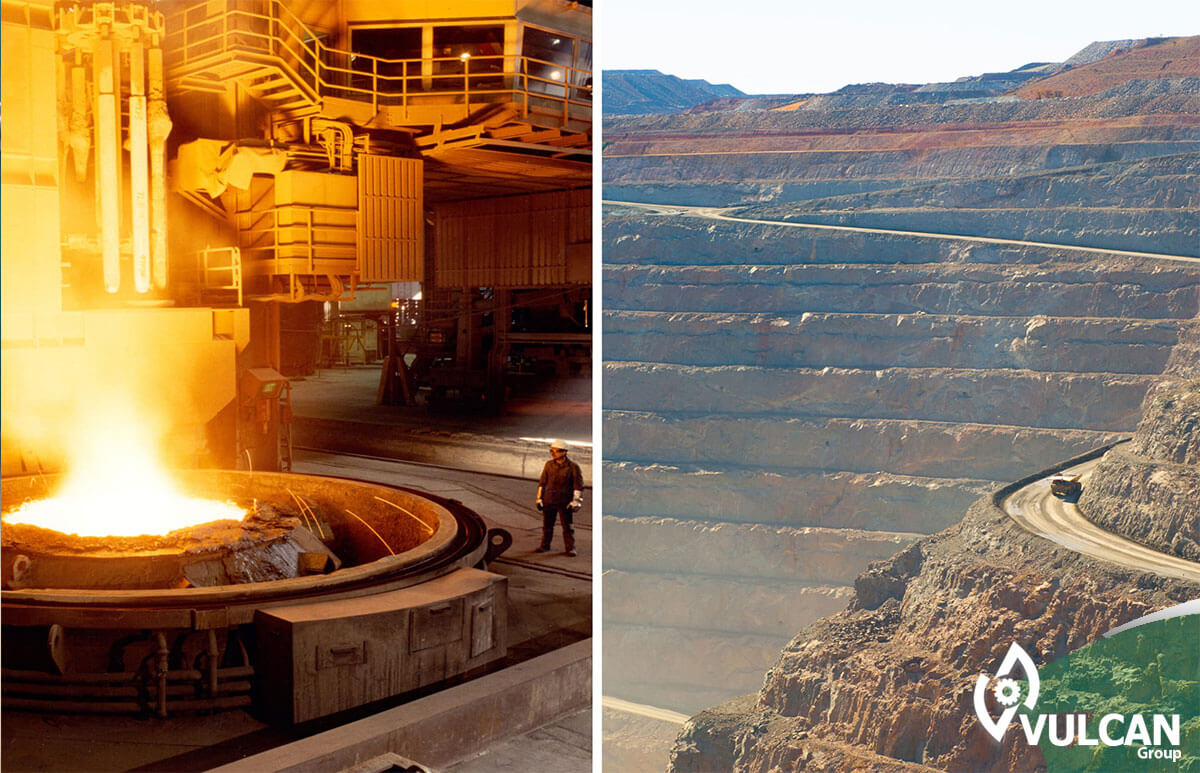
In metallurgical processes, different filter presses have many applications in accordance with different metallurgical processes.
- After leaching processes
- After cement processes
- After neutralization processes
- To pay for a chemical suspension
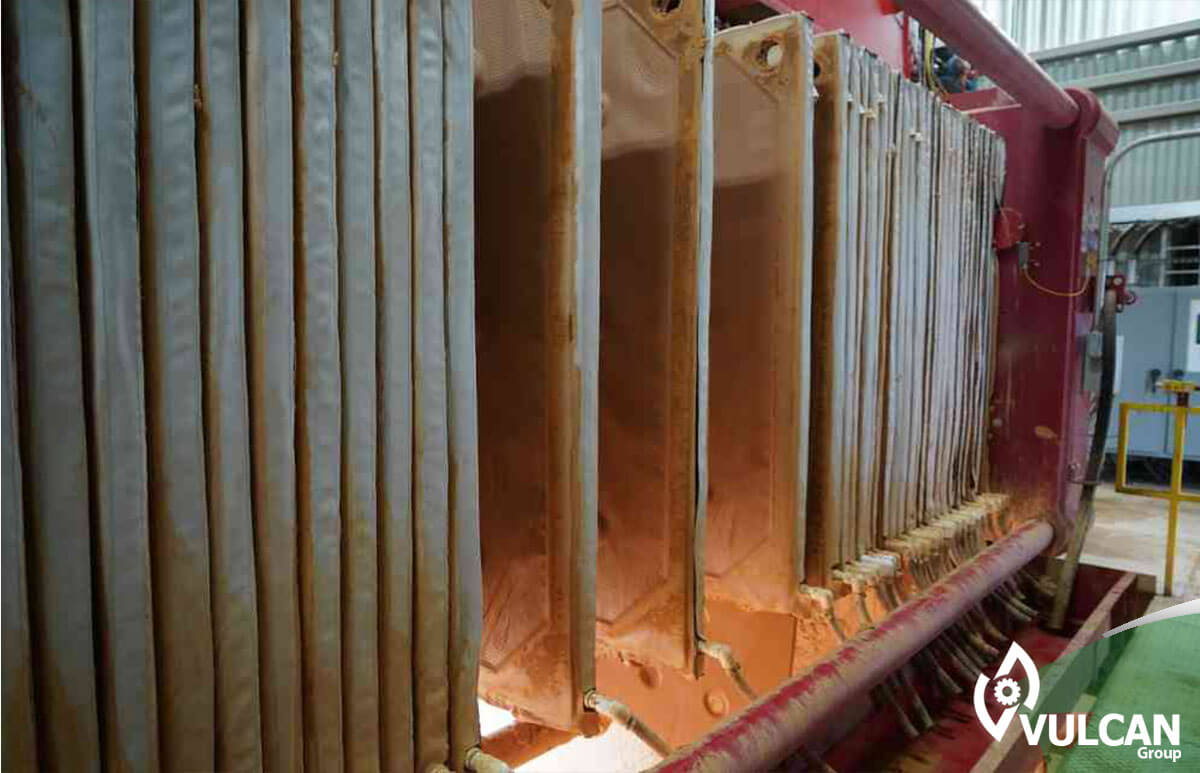
Chemical & Pharmaceutical Sector
Chemical
- Precision Chemistry
- Basic Chemistry
- Fertilizers and pesticides
- Pigments & Colors
- Plastic materials and synthetic resins
- Cosmetics, soap and fat and oil
- Petrochemical
- Surface Correction
- Lead recovery from batteries
Pharmaceutical Industry
- Vaccines
- Antibiotics
- Blood derivatives
- Pectins
Metallurgical and Chemical Industries
Cake Wash
Often in chemical and metallurgical sections, cake washing is essential for the removal of salt, residual acid, etc. For this reason, the filter press is equipped with the full membrane plates of the cake washing system.
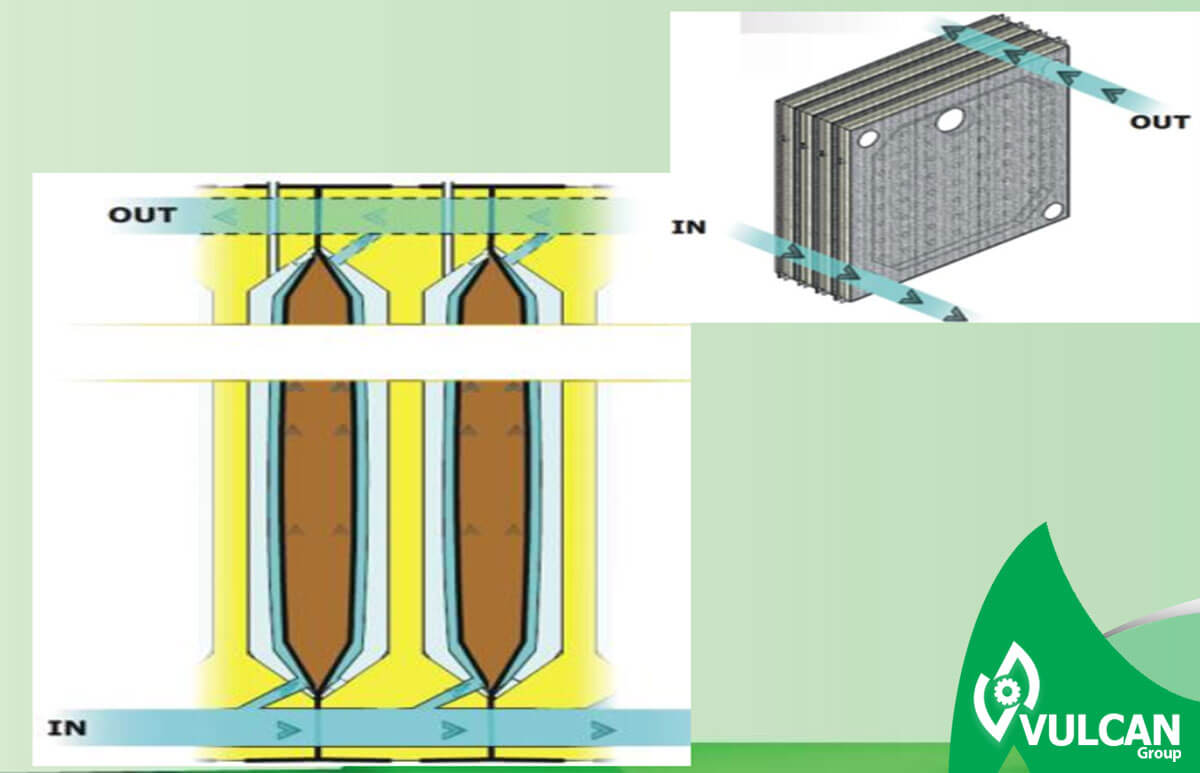
Food Industry
- Agriculture & Food
- Dairy Industry
- Distillation
- Slaughterhouse
- Sugar industry
- Planting Industry
- Oil Factory
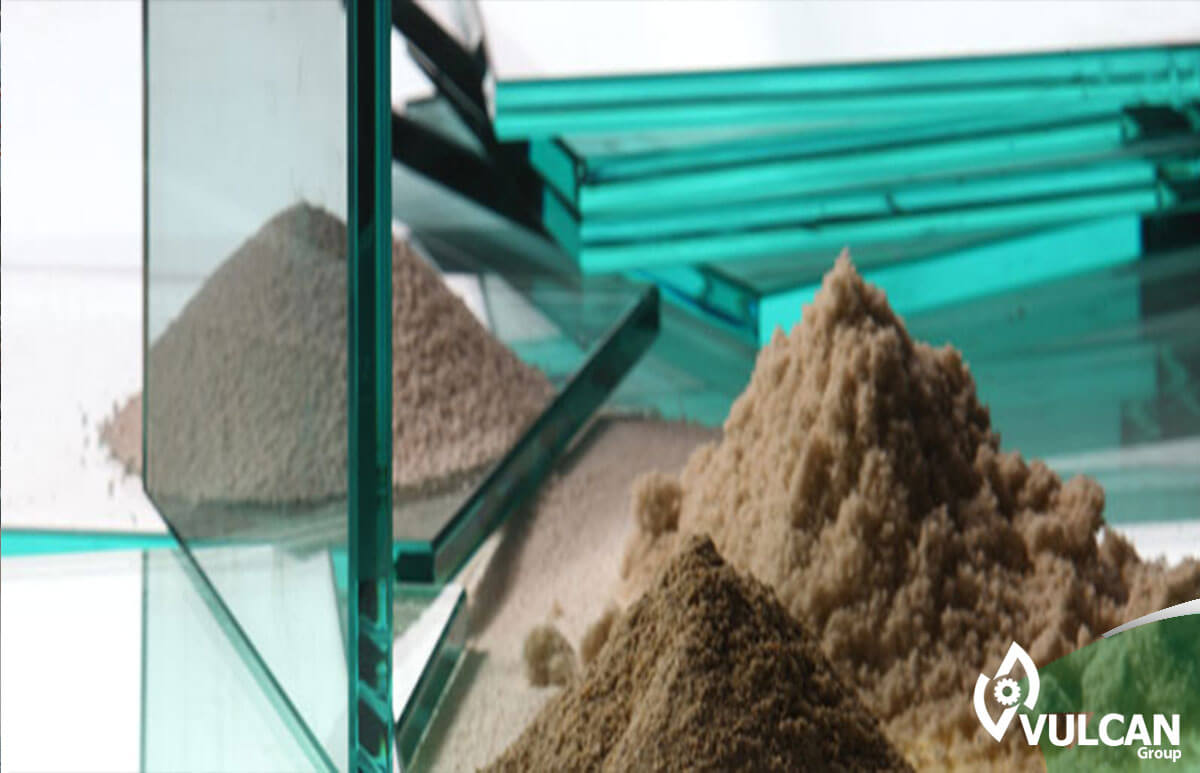
Ceramic glass and crystal industries
- Tile Production
- Sandstone Production
- Ceramic Mix Production (Gunpowder)
- Glass & Crystal
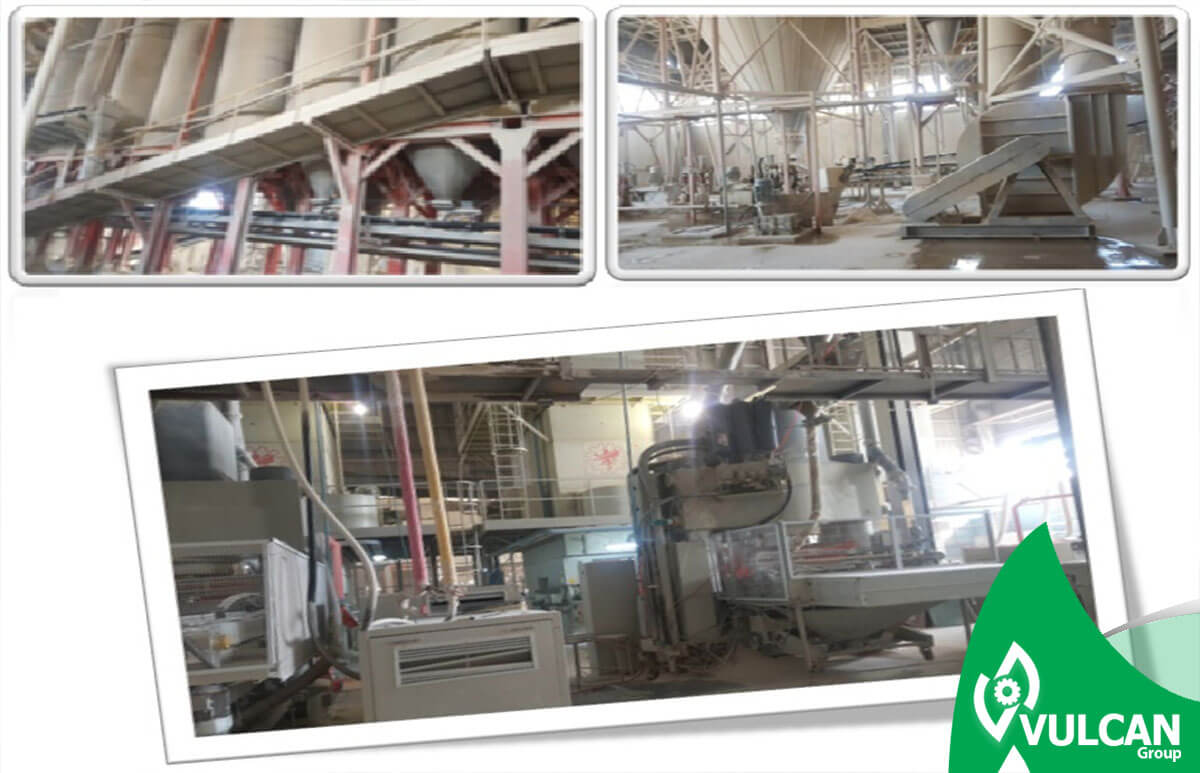
High temperature
When working with very viscous products (e.g. in the oil phase) filtration occurs at high temperatures (100°C <).
In such cases, filtration corresponds to:
– Using PVDF plates (polyvinylidene fluoride) with Wyton membrane;
– Injecting hot water into the plates to control the temperature and prevent heat shocks;
– Using PE coating (polyester) with rubber edges made of Wheaton
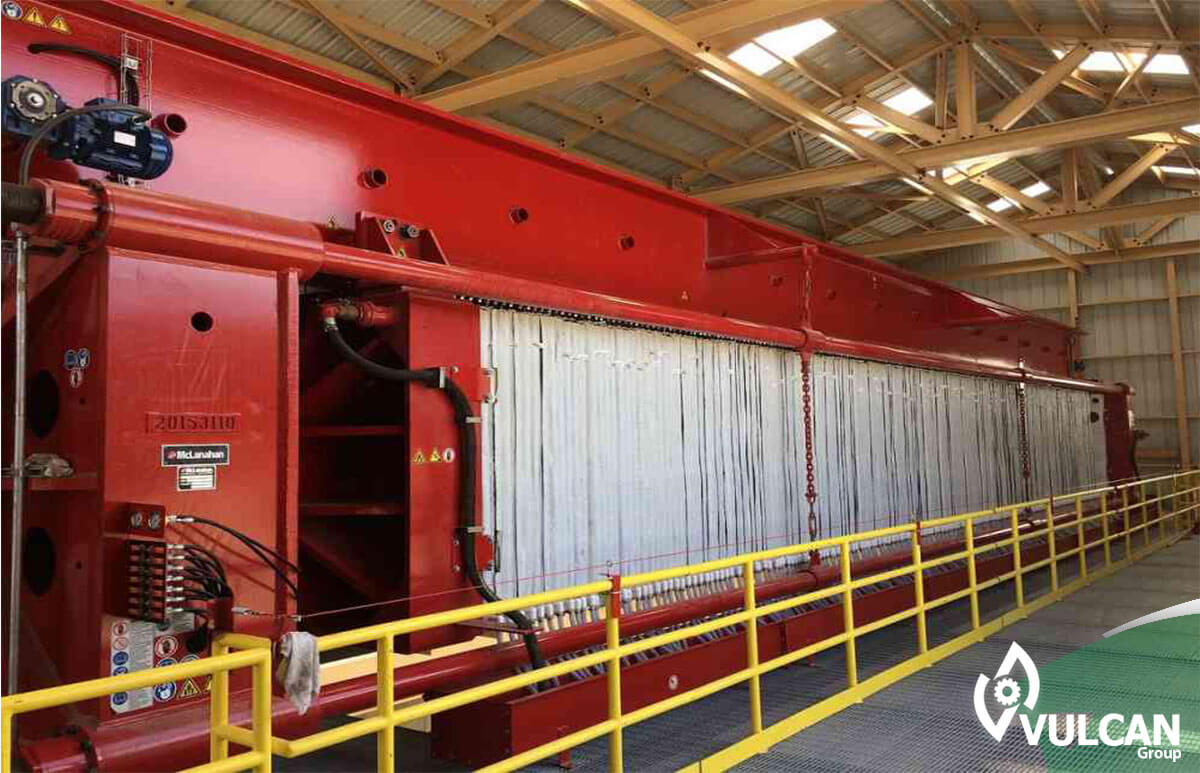
Industries including toxic cases
In the case of filtration of products containing toxic components, harmful vapors are likely to be released. For this filtration application, the filter separates the press from the surroundings by suction hoods, which removes vapors from the operator’s workplace.
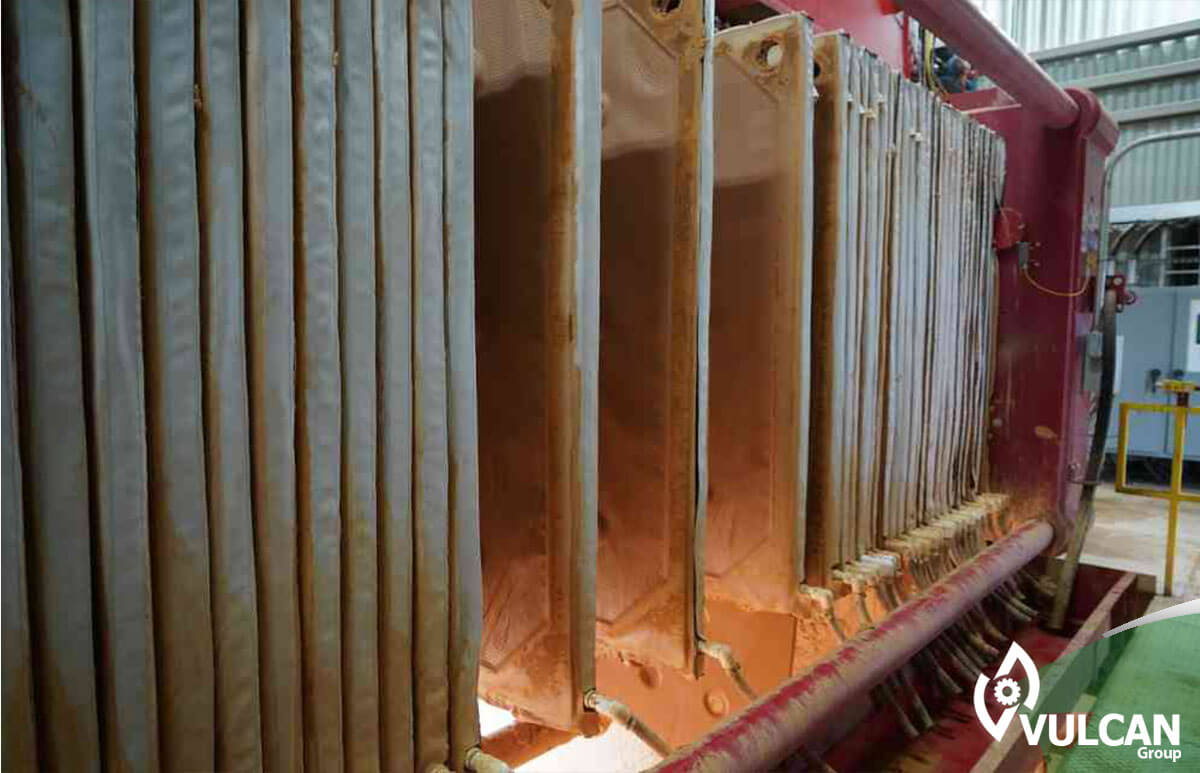
Explosives Industries (ATEX Filter Press)
Filters used in the chemical, petrochemical and pharmaceutical sectors often have to be equipped to operate in areas classified as explosion risk zones.
Some of the specified features are available as follows:
– Frame design suitable for ground electrical discharge;
– Using plates made of polypropylene and carbon mixtures to prevent deformation caused by electrostatic discharge;
– The use of coatings equipped with conductor fibers, in order to provide electrical discharge of the earth,
– Installing valves, electroloys and instrumentation that must be installed in the area specified by the regulations;
– Application of aluminum-free paint;
– Using low capacity conductor plastic materials.
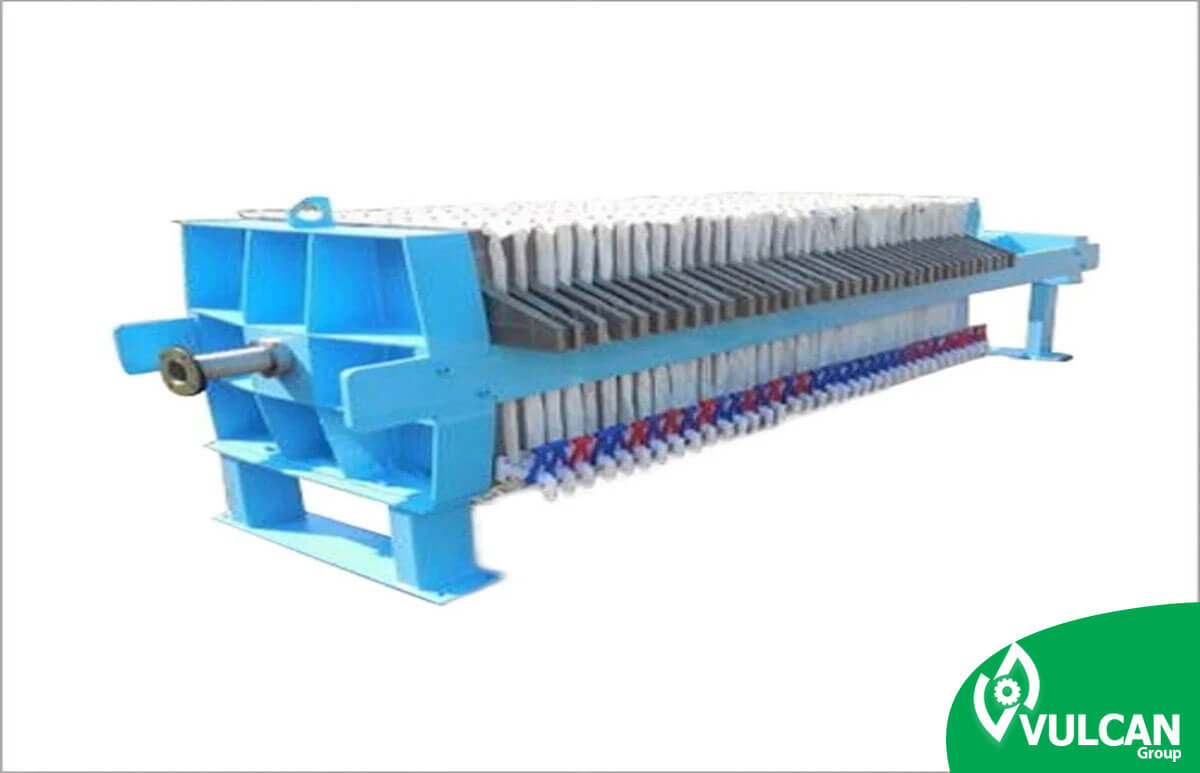
Industries with corrosive substances
When purifying metals, it is necessary to use suspensions with very low pH valves.
In such cases, filters are designed that have a few additional features:
- Protection headers through PP (polypropylene) plates fixed using sleeves of the same sex;
- Application of coatings, pipes and valves of polypropylene or plastic materials,
- Application of special epoxy paint to protect the frame against chemical damage;
- Protection of drip tray via epoxy tar (EPOXY-TAR);
- Installing oats or gaskets of Wheaton
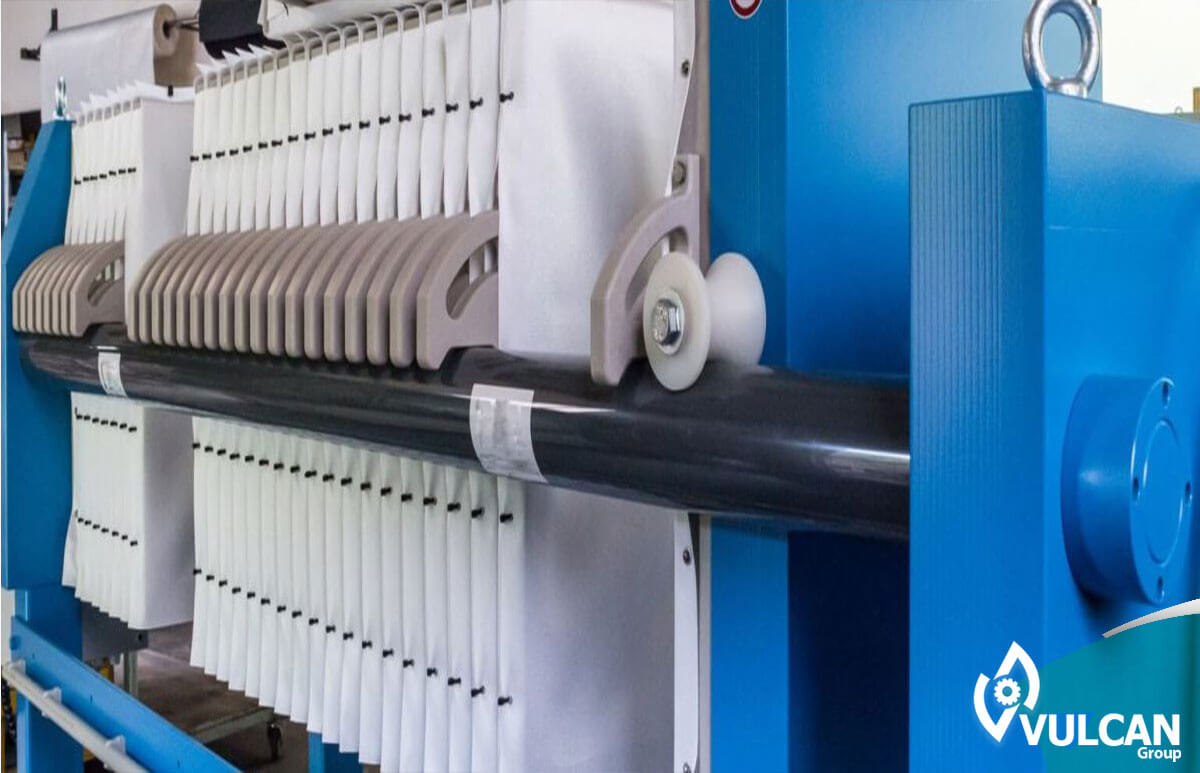
Kloyedha
In order to refine products with very low filtering capability and when separation from filter coating is difficult, manufacturers have provided new JETFILTER filter filter with the following specifications:
- “Page-to-page” feed using injectors;
- reduced chamber thickness,
- Simultaneous opening and closing of the animated screen from top to bottom to drain the molded section,
- Barrier cleaning to ensure that the mold is automatically drained from the coating,
- Cleanliness the barrier with high pressure water to remove any remaining part in the form of coatings.
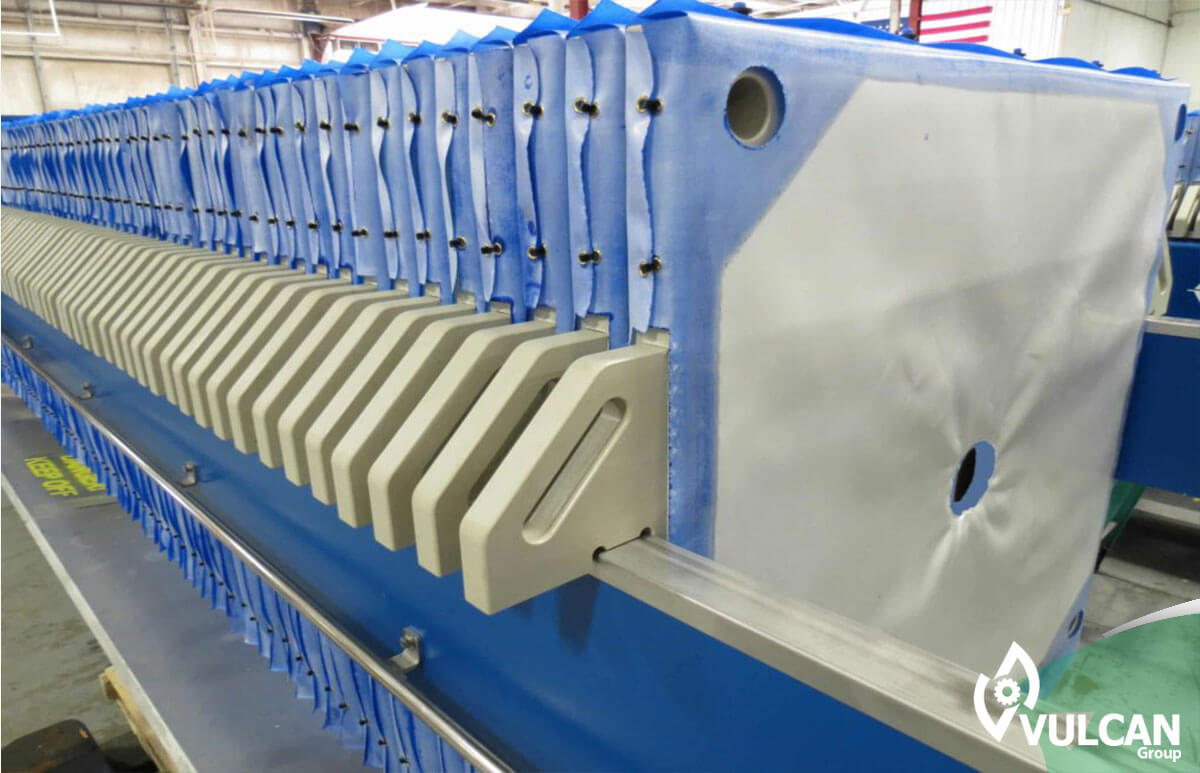
Low concentration
In the case of “polishing” when the filtered product contains a very low concentration of suspension solids, the main goal is to obtain a highly pure filtered flow. Infiltration, the following technical equipment is used:
Create a fossil food layer (presposed) on the fabric to ensure that the filtered material is completely free of solid particles within seconds of the filter starting.
The fossil food layer is carried out on-line to facilitate the percentage of solids processing, using “plates and frames” with very thin compartments, paper or cardboard filter components.
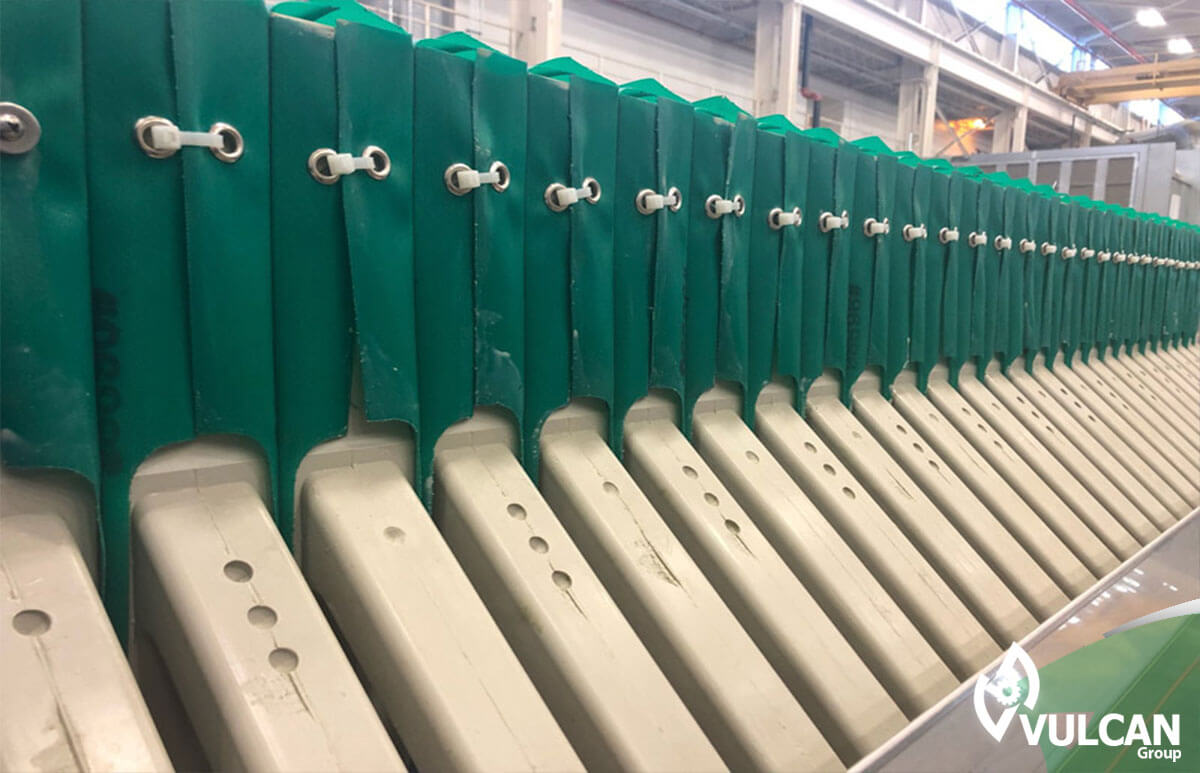
Cyndagi
In the mining sector (e.g. copper concentrate, zinc, lead, iron, coal, etc.) filtered sludge usually has high abrasion properties, high filterability and high feed rate due to its high concentration. Therefore, the filtration of certain devices, such as:
- The use of filter fabrics with special fibers with high mechanical strength;
- the use of special valves, made of anti-abrasive material;
- Feed pipe flux to eliminate the risk of sedimentation and blockages.
- Use centrifuge pumps against abrasion.
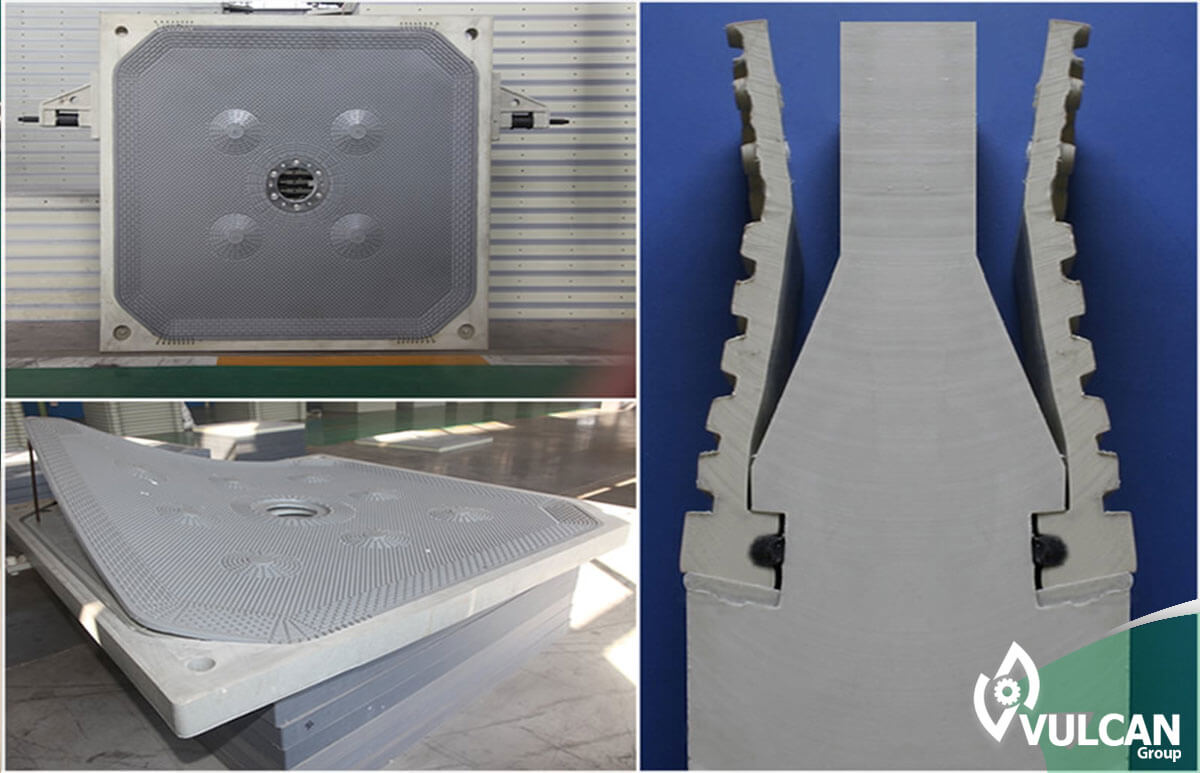
Conclusion
For each filtration plant, it is custom designed, manufactured and installed. In fact, each press filter is produced in accordance with the customer process data.
Online Order Registration Filter Press
To place an order, just enter your details and contact number, our experts will contact you as soon as possible.
Common questions about membranes filter press
The design and manufacture process of membranes filter press varies greatly according to different industries and is the type of project that determines the structure of these filters. As a result, Vulcan Sanat Sepahan Company produces most of its filter presses for different industries customized because at first a detailed industry-type expert is done and the best type of filter press is considered according to the type of work and then the production process is done.
Membran FilterPress in Vulcan Sanat Sepahan Group was researched and developed since January 1396 and after 500 people hours reached the production stage.
Related Content
How useful was this post?
Click on a star to rate it!
Average rating 5 / 5. Vote count: 3
No votes so far! Be the first to rate this post.